Warning, I am relatively new to the hobby, so dont look too close at the craftsmanship or you may see all my mistakes 
A few months back I was in Missouri visiting some family, and in my down time keeping an eye on craigslist for good deals in the area. Sure enough, there seemed to be a great deal for quarter sawn red oak lumber a few hours out in Arkansas. It was a few hour drive, but the deal was for 450 BF for $400, so not too bad for a bunch of quarter sawn oak if it turned out to be legit.
During some downtime, I decided to take the plunge and drive out and take a look and pick it up if it all looked legit. On site, it was in fact quarter sawn, but about 50/50 regular red oak, and some spalted red oak. I've heard of other woods getting spalted, maple being the most common, but never oak. Given the price point I decided to go for it. At the very least I figured it could be used for some sort of framing of something, or have it hidden somehow.
A thousand mile drive and some splinters later, I had a stack of lumber in my garage in one of the few remaining open spaces. The wood was air drying when I bought it and according to my meter around 20-22%MC. Being resourceful, and incredibly cheap (as indicated by my will to drive a few miles for some spalted oak in the middle of nowhere AK) I decided to try and fix the problem myself.
I had an old free standing AC that doubled as a dehumidifier and decided to set it up in the garage. Given the space involved, it didn't seem to be making much progress and appeared to mostly hold back moisture in the air to a small degree, and not have much impact to the lumber. Considering its also just a compressor running 24/7, I wasn't prepared to deal with an extra $50 jump to my electric bill for the next 6 months as this stuff dried out to a lower level.
Below is my feeble, yet successful attempt to try and dry the lumber a bit quicker to satisfy my impatience. A quick trip to home depot produced a large piece of thin plastic normally used for covering floors or large areas, and I used this to completely encase the lumber pile. I positioned the AC on one side of my lumber and used a spare hose to pipe the warm exhaust back into the pile. I let it run like this for about a week or two before swapping sides to try and dry the other half of the lumber. 3-4 weeks later my lumber went from 20%MC down to 9%. Against all odds, this actually worked.
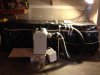
Now I had a stack of rough lumber. looking closely, you could see some of the spalting. its not very pronounced, but is there.
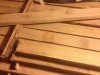
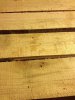
Next came planing everything down and picking the best boards for the table top. I was going for an L shape desk, so I knew the longest boards would be needed first, and I would make due with what was left over. During the air drying process there was a number of checks, twists and other splits that happened that made the longer pieces harder to come by.
Below we can see what the wood looks like after passing through the planer. This was my rough sizing before glue up to ensure I had enough.
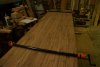
Once that was good came the glue, and lots of time. The board had some bends in it so I had to do one at a time due to a limited number of 24"+ clamps.
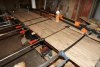
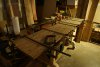
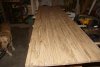
I also took out a piece of zebra wood for a comparison. Looking at them side by side, I feel like the oak is some sort of poorly constructed Chinese knock-off of real zebra wood
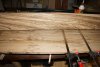
With the two pieces of the top complete, I could now focus on the cabinets. I had two needs. One needed to hold my server (rackmount IT server) and corresponding battery backups and extensive cabling. The second cabinet needed to hold a large number of files, essentially a traditional file cabinet.
The other requirement for the server side is that it remained open in order to allow good airflow and not overheat my equipment. The pics below are the cabinet coming together.
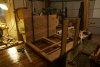
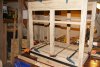
Next came the file cabinet. I decided to go with a shaker style and use the bandsaw to resaw some of the boards in order to get a nice mirror effect. I also included the pics with my square on top because lets face it, finally getting this thing to actually become square was quite the accomplishment and deserving of a picture!
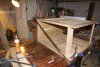

The last piece to come together was the center support to handle the corner of the "L". Again, it was a struggle at times, but eventually, enough clamps on top of clamps on top of clamps helped to ensure it was perfectly square all around.
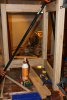
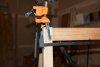
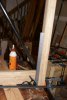
With the major pieces in place, now I needed to build the support structure to help keep the large table tops. I purposely designed this desk to hold a LOT of stuff on top. It needed to double as both a personal and work computer space, plus handle all the monitors that get thrown on top of it, in addition to other working equipment.
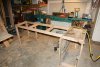
Once all pieces were in place, it was time for a dry fit so I could put a quarter round on the table top (primarily for comfort while typing) and ensure that I actually knew how to measure. As seen below, as it turns out, yes, I did figure out how to measure.
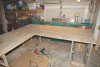
At that point, everything received a final sanding down to 320, and then was disassembled and put into my "finishing room". Some call it the dining room, I call it the one place the dog isnt allowed to go. (movers blankets helped protect the stuff I already have in there)
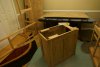
I really enjoy the look of natural wood, and while did play around with some stains and other finishes on sample scraps, nothing helped to really make the spalted lines look good IMO, so I stuck to a clear coat on everything.
The in an out of sanding and poly happened for a total of 3 separate coats, producing a nice high gloss shine in the final result.
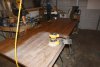
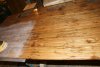
Finally, here are the results, showing a close up of the wood, the end grain near the edge of the top, the file cabinet ends, and some removable pieces for helping to hide wires (used 1 board for all of them, so the grain continues from piece to piece when they are in place.
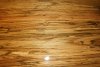
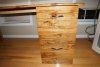
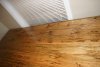
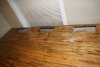
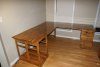
All in all, it was a good experience, and I am already looking forward to my next big furniture project. However, as a beginner I did learn some useful lessons throughout the way.
1. The table support structure should have been given a quarter round to not hurt my legs if I lift up on it
2. more clamps never hurt anything.
3. Use a larger drill bit to predrill my screws (used to secure the top to the cabinets and structure) My knuckles bleed from banging tight corners with a screw driver.
4. Triple check tools, and everything else for that matter is actually square.
-WD
A few months back I was in Missouri visiting some family, and in my down time keeping an eye on craigslist for good deals in the area. Sure enough, there seemed to be a great deal for quarter sawn red oak lumber a few hours out in Arkansas. It was a few hour drive, but the deal was for 450 BF for $400, so not too bad for a bunch of quarter sawn oak if it turned out to be legit.
During some downtime, I decided to take the plunge and drive out and take a look and pick it up if it all looked legit. On site, it was in fact quarter sawn, but about 50/50 regular red oak, and some spalted red oak. I've heard of other woods getting spalted, maple being the most common, but never oak. Given the price point I decided to go for it. At the very least I figured it could be used for some sort of framing of something, or have it hidden somehow.
A thousand mile drive and some splinters later, I had a stack of lumber in my garage in one of the few remaining open spaces. The wood was air drying when I bought it and according to my meter around 20-22%MC. Being resourceful, and incredibly cheap (as indicated by my will to drive a few miles for some spalted oak in the middle of nowhere AK) I decided to try and fix the problem myself.
I had an old free standing AC that doubled as a dehumidifier and decided to set it up in the garage. Given the space involved, it didn't seem to be making much progress and appeared to mostly hold back moisture in the air to a small degree, and not have much impact to the lumber. Considering its also just a compressor running 24/7, I wasn't prepared to deal with an extra $50 jump to my electric bill for the next 6 months as this stuff dried out to a lower level.
Below is my feeble, yet successful attempt to try and dry the lumber a bit quicker to satisfy my impatience. A quick trip to home depot produced a large piece of thin plastic normally used for covering floors or large areas, and I used this to completely encase the lumber pile. I positioned the AC on one side of my lumber and used a spare hose to pipe the warm exhaust back into the pile. I let it run like this for about a week or two before swapping sides to try and dry the other half of the lumber. 3-4 weeks later my lumber went from 20%MC down to 9%. Against all odds, this actually worked.
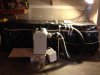
Now I had a stack of rough lumber. looking closely, you could see some of the spalting. its not very pronounced, but is there.
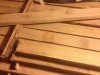
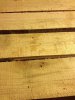
Next came planing everything down and picking the best boards for the table top. I was going for an L shape desk, so I knew the longest boards would be needed first, and I would make due with what was left over. During the air drying process there was a number of checks, twists and other splits that happened that made the longer pieces harder to come by.
Below we can see what the wood looks like after passing through the planer. This was my rough sizing before glue up to ensure I had enough.
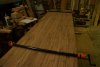
Once that was good came the glue, and lots of time. The board had some bends in it so I had to do one at a time due to a limited number of 24"+ clamps.
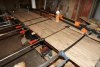
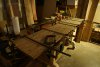
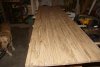
I also took out a piece of zebra wood for a comparison. Looking at them side by side, I feel like the oak is some sort of poorly constructed Chinese knock-off of real zebra wood
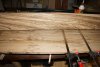
With the two pieces of the top complete, I could now focus on the cabinets. I had two needs. One needed to hold my server (rackmount IT server) and corresponding battery backups and extensive cabling. The second cabinet needed to hold a large number of files, essentially a traditional file cabinet.
The other requirement for the server side is that it remained open in order to allow good airflow and not overheat my equipment. The pics below are the cabinet coming together.
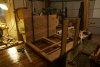
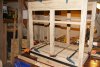
Next came the file cabinet. I decided to go with a shaker style and use the bandsaw to resaw some of the boards in order to get a nice mirror effect. I also included the pics with my square on top because lets face it, finally getting this thing to actually become square was quite the accomplishment and deserving of a picture!
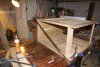

The last piece to come together was the center support to handle the corner of the "L". Again, it was a struggle at times, but eventually, enough clamps on top of clamps on top of clamps helped to ensure it was perfectly square all around.
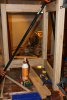
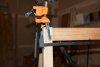
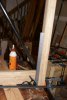
With the major pieces in place, now I needed to build the support structure to help keep the large table tops. I purposely designed this desk to hold a LOT of stuff on top. It needed to double as both a personal and work computer space, plus handle all the monitors that get thrown on top of it, in addition to other working equipment.
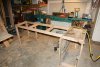
Once all pieces were in place, it was time for a dry fit so I could put a quarter round on the table top (primarily for comfort while typing) and ensure that I actually knew how to measure. As seen below, as it turns out, yes, I did figure out how to measure.
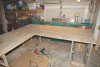
At that point, everything received a final sanding down to 320, and then was disassembled and put into my "finishing room". Some call it the dining room, I call it the one place the dog isnt allowed to go. (movers blankets helped protect the stuff I already have in there)
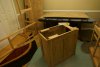
I really enjoy the look of natural wood, and while did play around with some stains and other finishes on sample scraps, nothing helped to really make the spalted lines look good IMO, so I stuck to a clear coat on everything.
The in an out of sanding and poly happened for a total of 3 separate coats, producing a nice high gloss shine in the final result.
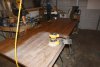
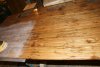
Finally, here are the results, showing a close up of the wood, the end grain near the edge of the top, the file cabinet ends, and some removable pieces for helping to hide wires (used 1 board for all of them, so the grain continues from piece to piece when they are in place.
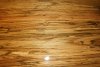
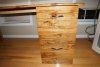
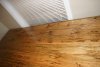
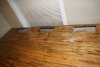
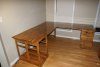
All in all, it was a good experience, and I am already looking forward to my next big furniture project. However, as a beginner I did learn some useful lessons throughout the way.
1. The table support structure should have been given a quarter round to not hurt my legs if I lift up on it
2. more clamps never hurt anything.
3. Use a larger drill bit to predrill my screws (used to secure the top to the cabinets and structure) My knuckles bleed from banging tight corners with a screw driver.
4. Triple check tools, and everything else for that matter is actually square.
-WD