I have basically completed my new workbench, save for a few cosmetic details. Since it seems that someone here is almost always building a workbench, I thought I would review some of the design and construction options and decisions I went through in building my “Big Ash Workbench.” This will probably be the proverbial “too much information” for many folks, but perhaps someone will get something out of it.
In planning my bench, I read a number of writings by Christopher Schwartz, looked at lots of other people’s benches on line, and got a copy of Lon Schleining’s book, “The Workbench, A Complete Guide to Creating Your Perfect Bench.” I also looked at the information that Benchcrafted has on their website.
There are some amazing workbenches out there. Every time I saw a great looking bench I would want to pattern mine after it. I finally made the decision to build kind of a hybrid split-top Roubo style bench.
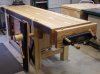
The Big Ash Workbench
Some of the basic dimensions:
Overall: 95” long x 29” wide x 34 5/8” tall. (the height makes the bench just a hair lower than my table saw, allowing oversize lumber to the left of the blade to rest on the workbench.)
Top is 2 pieces 13 ¼” wide and 3 5/8" thick each, with a 2 ½” gap between. (a “gap stop” fills the space.)
The legs are about 4 ¾” x 4 ½”. The top rests on 3 ½” x 3 ¾” cross pieces mortised into the legs.
The bench must weigh something in the neighborhood of 500 pounds. I began with about 165 board feet of rough ash lumber, and about 15 board feet of walnut. Wood for the leg vise and the twin screw end vise are walnut and red oak, respectively.
After checking out every type of vise available, I ended up with a Veritas twin screw end vise, which is the full width of the bench, and a leg vise with a Lake Erie Toolworks wooden screw. The leg vise was one element that took a bit of rethinking in construction – more on that later. I still have an Acme screw which was supposed to have been for a shoulder vise. That was another changed decision during construction.
One of the intriguing details about Roubo’s bench is the double through-tenon attaching the leg to the top. One tenon appears to be rectangular, and the other is dovetailed.
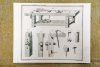
Roubo's Workbench Drawings
I liked the dovetail tenon as a decorative detail, and designed my bench with the legs made up of 4 boards, each an inch and an eighth thick. The corresponding part of the top is also made up of inch and an eighth stock. So, the outermost board in the leg and the top are made with the dovetail. The next course has the top sitting on top of the leg. The next course would have been where Roubo had a through dovetail, and one final course of inch and an eighth stock again has the top sitting directly on the leg.
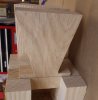
Leg Tenon Construction
Instead of a regular through tenon, I wanted to do something different. So, messing with a little model I mocked up, I came up with something I am calling a “double-splined dovetail through tenon.” The narrow bottom of the “Vee” in the top is the same width as the wide part of the “Vee” on the leg’s tenon. The leg has a ¼” tall portion of the tenon which allows the pieces to register properly. The two splines are driven down into the openings, and the top is not coming off anymore. It locks the pieces together very tightly. I am sure this joint has a name and has been used before, but I haven’t seen it anywhere. This is the mock-up I was playing with when I came up with this design.
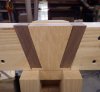
"Double Splined Dovetail Through Tenon"
With the different tenons and mortises, there were a lot of interesting cuts.
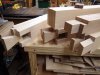
Legs and Undercarriage Components
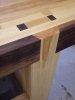
Finished Leg Tenon Detail
The rest of the top was made of 8/4 stock. I basically built the undercarriage first, then constructed the top in place, a piece or two at a time. In addition to the through tenons, I put 4 bolts up from the cross-pieces into the top. These go through oversize holes, allowing the top to expand and contract. The entire top began as plane sawn stock which has been cut to the width of the top’s thickness, and placed on edge, resulting in most of the lumber being rift or quarter-sawn, in effect.
The bench was built around the little cabinet underneath, a piece that I had used under my previous bench. It provides very handy storage.
Installing the twin screw tail vise was pretty straight-forward. I used 8/4 red oak and constructed the jaws to be 29” x 9”.
The leg vise was a bit more eventful. First, the Lake Erie Toolworks screw is a work of art. It is 2 ½” in diameter, and the entire piece is about 24 inches long, including the hub. It is BIG! The wooden nut is also impressive, and getting the nut attached to the leg was made easier by my laminated legs. I was able to “mortise” the nut into the legs by cutting the laminated pieces before gluing them up. I also was able to insert “Tee nuts” between the laminations, so the nut is held on with screws, and can be removed should it ever need to be. Once it was finished and waxed, the Lake Erie screw is amazingly smooth and easy to turn. And it grips REALLY tight.
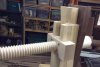
Fitting the Leg Vise Nut
My original intention was to use a 35mm steel rod with a linear bearing at the bottom of the leg vise. I had read about a fellow who had used a linear bearing at the bottom with an Acme screw at the top. He had advised installing the rod and bearing at about a 1 degree angle. Trouble is, the wooden screw has very little play in it, and even a 1 degree angle on the steel rod caused the wooden screw to bind. I did not find that the linear bearing helped much in keeping the vise chop parallel with the leg. The bottom of the chop still came in too far, and required blocking to get good clamp pressure.
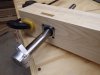
Steel Rod and Linear Bearing
So, after looking at several alternatives, I removed the linear bearing and installed Benchcrafted’s “Criss-Cross” Retro. This ingenious device works absolutely perfectly. The cross actually supports the chop throughout its entire range of motion, keeping the threads aligned perfectly. The bottom of the vise has just a hint of “toe-out,” which keeps the jaw surface dead flat when tightened.
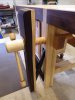
Lake Erie Toolworks Screw and Benchcrafted Criss-Cross
I went with square dog holes, building them into the top as it was being built. There are two rows of holes, each with a resident dog. The holes are set at a 2 degree angle toward the end vise on both sides of the bench, in about 2 ½” in from the edge. I felt the advantage of the square holes was being able to construct it without there being any holes, since the dogs fill the holes and have a positive stop, which keeps them from going below the surface. Each dog has a thin angled “spring” that holds it in place when deployed. Here is a photo of cutting the dog holes:
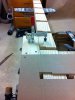
Cutting the Bench Dog Holes
And here is one of the dogs:
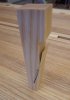
Bench Dog
One of the more odd decisions I made was to locate both the end vise and the leg vise on the same end of the bench. That is based on the way I have used my previous bench, and my shop layout. I am not sure I would recommend that to anyone else, but it works for me.
I built a little sliding deadman to go with the leg vise, but I am not sure how often I will use it. When I put in the long stretcher piece on the front side, I built an angled top into the piece, so the deadman could slide along easily.
Flattening the top took a bit of work. I had a couple of aluminum extrusions that are very accurate, and I used them to help find the high and low spots. I then worked it with a jack plane. And when it was pretty close, I broke out the belt sander. The final surface was achieved with a card scraper. (Actually, several scrapers. Those things get very hot working that much surface, and I would let one cool and move to another.)
The gap-stop is a removable piece that fits in the slot between the top pieces. It can either be level with the top surface, or can be turned over to extend about half an inch above the work surface, to act as a stop with short pieces of stock. The gap-stop can also be removed completely to allow a clamp to be secured in the center of the top.
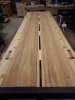
Top with Gap Stop
I put a coat of boiled linseed oil on everything. I wasn’t going to put it on the top, but it looked so good everywhere else, that I couldn’t help myself. I am sure it will get worn off the top before long.
So far, I am very happy with the bench. My main complaint with my old bench was that it would move and “walk” during some operations. This bench doesn’t move, its rock solid.
The next question I will ponder is, what should I have done differently? There isn’t anything I would change at this point. I am happy with the material, the size, the hardware, and even how it looks. I hope to get a lot of years of use out of it.
In planning my bench, I read a number of writings by Christopher Schwartz, looked at lots of other people’s benches on line, and got a copy of Lon Schleining’s book, “The Workbench, A Complete Guide to Creating Your Perfect Bench.” I also looked at the information that Benchcrafted has on their website.
There are some amazing workbenches out there. Every time I saw a great looking bench I would want to pattern mine after it. I finally made the decision to build kind of a hybrid split-top Roubo style bench.
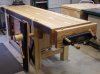
The Big Ash Workbench
Some of the basic dimensions:
Overall: 95” long x 29” wide x 34 5/8” tall. (the height makes the bench just a hair lower than my table saw, allowing oversize lumber to the left of the blade to rest on the workbench.)
Top is 2 pieces 13 ¼” wide and 3 5/8" thick each, with a 2 ½” gap between. (a “gap stop” fills the space.)
The legs are about 4 ¾” x 4 ½”. The top rests on 3 ½” x 3 ¾” cross pieces mortised into the legs.
The bench must weigh something in the neighborhood of 500 pounds. I began with about 165 board feet of rough ash lumber, and about 15 board feet of walnut. Wood for the leg vise and the twin screw end vise are walnut and red oak, respectively.
After checking out every type of vise available, I ended up with a Veritas twin screw end vise, which is the full width of the bench, and a leg vise with a Lake Erie Toolworks wooden screw. The leg vise was one element that took a bit of rethinking in construction – more on that later. I still have an Acme screw which was supposed to have been for a shoulder vise. That was another changed decision during construction.
One of the intriguing details about Roubo’s bench is the double through-tenon attaching the leg to the top. One tenon appears to be rectangular, and the other is dovetailed.
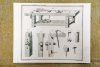
Roubo's Workbench Drawings
I liked the dovetail tenon as a decorative detail, and designed my bench with the legs made up of 4 boards, each an inch and an eighth thick. The corresponding part of the top is also made up of inch and an eighth stock. So, the outermost board in the leg and the top are made with the dovetail. The next course has the top sitting on top of the leg. The next course would have been where Roubo had a through dovetail, and one final course of inch and an eighth stock again has the top sitting directly on the leg.
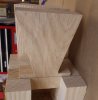
Leg Tenon Construction
Instead of a regular through tenon, I wanted to do something different. So, messing with a little model I mocked up, I came up with something I am calling a “double-splined dovetail through tenon.” The narrow bottom of the “Vee” in the top is the same width as the wide part of the “Vee” on the leg’s tenon. The leg has a ¼” tall portion of the tenon which allows the pieces to register properly. The two splines are driven down into the openings, and the top is not coming off anymore. It locks the pieces together very tightly. I am sure this joint has a name and has been used before, but I haven’t seen it anywhere. This is the mock-up I was playing with when I came up with this design.
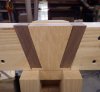
"Double Splined Dovetail Through Tenon"
With the different tenons and mortises, there were a lot of interesting cuts.
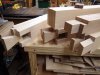
Legs and Undercarriage Components
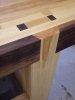
Finished Leg Tenon Detail
The rest of the top was made of 8/4 stock. I basically built the undercarriage first, then constructed the top in place, a piece or two at a time. In addition to the through tenons, I put 4 bolts up from the cross-pieces into the top. These go through oversize holes, allowing the top to expand and contract. The entire top began as plane sawn stock which has been cut to the width of the top’s thickness, and placed on edge, resulting in most of the lumber being rift or quarter-sawn, in effect.
The bench was built around the little cabinet underneath, a piece that I had used under my previous bench. It provides very handy storage.
Installing the twin screw tail vise was pretty straight-forward. I used 8/4 red oak and constructed the jaws to be 29” x 9”.
The leg vise was a bit more eventful. First, the Lake Erie Toolworks screw is a work of art. It is 2 ½” in diameter, and the entire piece is about 24 inches long, including the hub. It is BIG! The wooden nut is also impressive, and getting the nut attached to the leg was made easier by my laminated legs. I was able to “mortise” the nut into the legs by cutting the laminated pieces before gluing them up. I also was able to insert “Tee nuts” between the laminations, so the nut is held on with screws, and can be removed should it ever need to be. Once it was finished and waxed, the Lake Erie screw is amazingly smooth and easy to turn. And it grips REALLY tight.
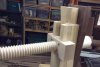
Fitting the Leg Vise Nut
My original intention was to use a 35mm steel rod with a linear bearing at the bottom of the leg vise. I had read about a fellow who had used a linear bearing at the bottom with an Acme screw at the top. He had advised installing the rod and bearing at about a 1 degree angle. Trouble is, the wooden screw has very little play in it, and even a 1 degree angle on the steel rod caused the wooden screw to bind. I did not find that the linear bearing helped much in keeping the vise chop parallel with the leg. The bottom of the chop still came in too far, and required blocking to get good clamp pressure.
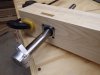
Steel Rod and Linear Bearing
So, after looking at several alternatives, I removed the linear bearing and installed Benchcrafted’s “Criss-Cross” Retro. This ingenious device works absolutely perfectly. The cross actually supports the chop throughout its entire range of motion, keeping the threads aligned perfectly. The bottom of the vise has just a hint of “toe-out,” which keeps the jaw surface dead flat when tightened.
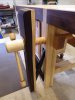
Lake Erie Toolworks Screw and Benchcrafted Criss-Cross
I went with square dog holes, building them into the top as it was being built. There are two rows of holes, each with a resident dog. The holes are set at a 2 degree angle toward the end vise on both sides of the bench, in about 2 ½” in from the edge. I felt the advantage of the square holes was being able to construct it without there being any holes, since the dogs fill the holes and have a positive stop, which keeps them from going below the surface. Each dog has a thin angled “spring” that holds it in place when deployed. Here is a photo of cutting the dog holes:
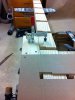
Cutting the Bench Dog Holes
And here is one of the dogs:
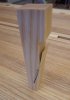
Bench Dog
One of the more odd decisions I made was to locate both the end vise and the leg vise on the same end of the bench. That is based on the way I have used my previous bench, and my shop layout. I am not sure I would recommend that to anyone else, but it works for me.
I built a little sliding deadman to go with the leg vise, but I am not sure how often I will use it. When I put in the long stretcher piece on the front side, I built an angled top into the piece, so the deadman could slide along easily.
Flattening the top took a bit of work. I had a couple of aluminum extrusions that are very accurate, and I used them to help find the high and low spots. I then worked it with a jack plane. And when it was pretty close, I broke out the belt sander. The final surface was achieved with a card scraper. (Actually, several scrapers. Those things get very hot working that much surface, and I would let one cool and move to another.)
The gap-stop is a removable piece that fits in the slot between the top pieces. It can either be level with the top surface, or can be turned over to extend about half an inch above the work surface, to act as a stop with short pieces of stock. The gap-stop can also be removed completely to allow a clamp to be secured in the center of the top.
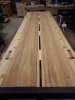
Top with Gap Stop
I put a coat of boiled linseed oil on everything. I wasn’t going to put it on the top, but it looked so good everywhere else, that I couldn’t help myself. I am sure it will get worn off the top before long.
So far, I am very happy with the bench. My main complaint with my old bench was that it would move and “walk” during some operations. This bench doesn’t move, its rock solid.
The next question I will ponder is, what should I have done differently? There isn’t anything I would change at this point. I am happy with the material, the size, the hardware, and even how it looks. I hope to get a lot of years of use out of it.