About two months later than I'd originally intended, but I'm finally pretty much done with this new CNC router. My first one was an all MDF build (heck of a lot cheaper than metal, and could always reuse the movement parts on a metal build), about 3'x4' cut area. Definitely a usable machine, but the flex caused by it being mdf, and using lower quality linear slides (skate bearings and angle iron) limited its speed and accuracy. So a few months back, I decided I wanted a second machine, designed to be as stiff and fast as I could make it, but sized so I could put it on my desk in my office so I don't have to run out to the shop to cnc things.
Once I decided to make it, I also decided I would document everything and publish a guide on building it. I need to finish that off still, but its about 2/3 written, 20 pages of pure text already, and I've got probably 100+ photos from the build to add to all the instructions, plus formatting, etc, so I suspect my "guide" is going to be more of a book
All that's left now is to wire up the electronics, and let it cut the final aluminum router mounts to replace the temp wood ones - I didn't feel like hand routing a 3.5" diameter hole in 3/4" aluminum plate
. Should have it up and running tomorrow afternoon.
As to specs - framing is 3"x3" 15 series 8020, with 1/2 and 3/4" aluminum plate for the gantry carriage, chinese 15mm profile rails and bearing blocks, 425oz nema23 stepper motors, and 1/2" acme leadscrews with 0.5" lead. Cut area is just a hair over 12"x12" with 3-4" of Z clearance.
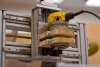
Once I decided to make it, I also decided I would document everything and publish a guide on building it. I need to finish that off still, but its about 2/3 written, 20 pages of pure text already, and I've got probably 100+ photos from the build to add to all the instructions, plus formatting, etc, so I suspect my "guide" is going to be more of a book
All that's left now is to wire up the electronics, and let it cut the final aluminum router mounts to replace the temp wood ones - I didn't feel like hand routing a 3.5" diameter hole in 3/4" aluminum plate
As to specs - framing is 3"x3" 15 series 8020, with 1/2 and 3/4" aluminum plate for the gantry carriage, chinese 15mm profile rails and bearing blocks, 425oz nema23 stepper motors, and 1/2" acme leadscrews with 0.5" lead. Cut area is just a hair over 12"x12" with 3-4" of Z clearance.
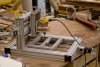
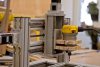
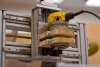