My wife wants a sitting place in the bathroom. Not a shower seat but a place to sit while dressing, etc. I thought of a small blanket chest to match the cherry vanity I built for the bathroom a couple of years back. I worked out this design to fit into the space. It’s about 26” x 20” x 21” high—a little higher than a side chair.
The top will be hinged over a storage space and there is a drawer below the storage. The construction is frame and panel (or post and panel—whatever the correct term).
I’ve just started construction and will post photos as I move along.
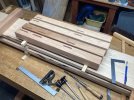
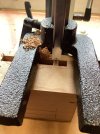
Starting with the legs milled to size and still square I laid out and cut the mortises using a bench mortiser, cleaned the mortise out with chisel and made a sample block from a leg cut-off. The sample lets me try the tenons for fit without using the legs.
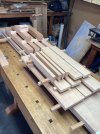
After milling the rails to size I cut the tenons using a box joint set on table saw. Rails are cut to tenon shoulder length plus 1 1/2“ since I’m using 3/4” tenons on this job. I’ve used different methods but this seems to work best for me.
Testing the tenon setup for tenon thickness and centering. I use a cutoff from a milled rail to dial in the tablesaw setup. I'm Using 5/16”mortises and tenons here.
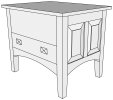
I’ve just started construction and will post photos as I move along.
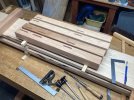
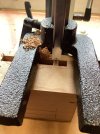
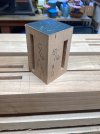
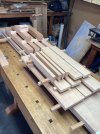
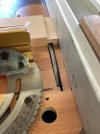
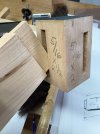
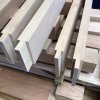
Last edited: