Got an email from Rockler about a CNC tool. https://shapertools.com/
Wanted to see how hard it would be to design something for it. So followed this tutorial
http://www.highlandwoodworking.com/woodnews/2009october/sketchup.html
Can someone explain how to do the following? It's driving me nuts as I don't know how to get one face of the different components on the same plane. Hoping there is a plugin or extension that does most of it and then lets me move things around after.
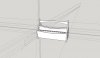
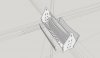
I'd like to do some Greene and Greene style furniture and am thinking this would be a great way to create templates.
Thanks
Wanted to see how hard it would be to design something for it. So followed this tutorial
http://www.highlandwoodworking.com/woodnews/2009october/sketchup.html
Can someone explain how to do the following? It's driving me nuts as I don't know how to get one face of the different components on the same plane. Hoping there is a plugin or extension that does most of it and then lets me move things around after.
Using the "move" and "rotate" tools, lay all of the parts of your toolbox onto a single flat surface, staying inside your workspace. I must admit that I am not very adept at this part of the process, though whether you are renting time on one of these machines or having someone else produce it for you, you will most likely be able to find someone to help you with the technical parts of this step. |
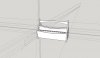
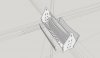
I'd like to do some Greene and Greene style furniture and am thinking this would be a great way to create templates.
Thanks