Picked up a Jtech 14 watt laser today for a good price secondhand.
If you're in need of a laser to complement a cnc and need something bigger than one of the little Chinese gantry machines, it's a solid option. I'm not a huge fan of a $1k laser diode unit (I paid around $600, but msrp is way up there) coming with a 3d printed housing, but hey, if it works it works.
They have a higher power version- the 24 watt quad (which apparently is closer to 28 watt) but for the delta in price I'll settle for this.
Just a few test burns of random logos and things tonight to see what it can and can't do. Cutting is a secondary consideration for a diode IMO- they really are better suited to engraving- but this one gets through 3/8 walnut with relative ease. 5 passes at 10 IPM and the parts fell right out. Sure, I could do it with an endmill in a twentieth of the time, but that's not the point. Sometimes you need that Itty bitty kerf. With the way diode laser setups are improving though I won't be surprised to see 40 watt or greater true output before long. Although the safety aspect of that is kind of concerning in an unenclosed environment...
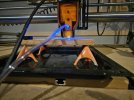
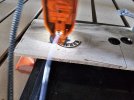
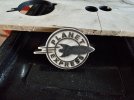
If you're in need of a laser to complement a cnc and need something bigger than one of the little Chinese gantry machines, it's a solid option. I'm not a huge fan of a $1k laser diode unit (I paid around $600, but msrp is way up there) coming with a 3d printed housing, but hey, if it works it works.
They have a higher power version- the 24 watt quad (which apparently is closer to 28 watt) but for the delta in price I'll settle for this.
Just a few test burns of random logos and things tonight to see what it can and can't do. Cutting is a secondary consideration for a diode IMO- they really are better suited to engraving- but this one gets through 3/8 walnut with relative ease. 5 passes at 10 IPM and the parts fell right out. Sure, I could do it with an endmill in a twentieth of the time, but that's not the point. Sometimes you need that Itty bitty kerf. With the way diode laser setups are improving though I won't be surprised to see 40 watt or greater true output before long. Although the safety aspect of that is kind of concerning in an unenclosed environment...
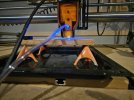
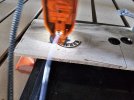
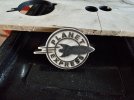