I am considering purchasing a large Brazilian Satinwood cookie (about 7 ft x 5.5 ft x about 8" thick max dimension). Before committing to the endeavor I'd like help thinking it through.
I traveled to Asheville Wed-Thursday and visited the usual woodworking suspects. At Scrounger's Paradise, they had three "Mickey Mouse" shaped Brazilian Satinwood Cookies. They have ben air drying at least 4 years. They measure less than 10% moisture at the surface (though they are 6-8" thick).
The pieces are "speaking to me" and I'd like to purchase the one pictured and make it into a dining table.
Here is the specific piece of wood:
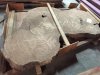
I am thinking these are the main considerations:
So the cookie is not cheap and the project is significant.
What are your thoughts?
I traveled to Asheville Wed-Thursday and visited the usual woodworking suspects. At Scrounger's Paradise, they had three "Mickey Mouse" shaped Brazilian Satinwood Cookies. They have ben air drying at least 4 years. They measure less than 10% moisture at the surface (though they are 6-8" thick).
The pieces are "speaking to me" and I'd like to purchase the one pictured and make it into a dining table.
Here is the specific piece of wood:
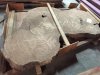
I am thinking these are the main considerations:
- Moisture/stability/structural soundness - seems generally ok
- Moving- I have trailer with sufficient weight limit. They have machinery to load on trailer. I need to figure out how to get it off
- Work area - need to figure out where to work on this thing. It will take up a lot of space until completed and ready for use. Also work on floor or place on work support?
- Flattening, preparing surface - all edge grain on the surface; options:
- Winding sticks and hand planes?
- Hand power planer?
- Router sled - large span - design would need extra rigidity than common designs?
- Edge preparation goals and execution
- Stabilize cracks where necessary, bow ties etc
- Finish - Want a finish that is durable so that we don't need to cover with dining table cloth
- Base-
- complicated shape makes base design somewhat problematic. Slab shape would seat a lot of people but I wouldn't want the base to block people's legs
- need to account for movement potentially in 2 directions unless I am certain the design allows movement perpendicular to tangent of growth rings in cookie
- Needs to be 'easy' to break down and align given weight of top
- Metal vs wood base and a host of design issues
- Moving to room and setting up
So the cookie is not cheap and the project is significant.
What are your thoughts?