I built a bed for my wife and I this past spring (10 months ago) out of regular old pine from Lowes. My shop is not climate controlled and I didn't acclimate the wood inside our home before building the bed. The wood hasn't moved much, the piece is rustic in style anyway, so the joints weren't perfect to begin with. Some friends liked our bed and asked me to build one for them, I did theirs in the summer and it still looks great now, just a slight movement in some of the boards. I made a few beds this fall with the same design.
The headboard and frame are not connected and the headboard is attached to the wall.
I recently had someone ask me to make a bed from a different design where the frame and headboard are connected. My concern is that the wood movement will cause the bed to not work out as nicely for these people as the other design did for us. I know you are supposed to acclimate the wood in its final environment before working with it, but how do I do that with an entire bed? The only things I know to do are to make the shop climate controlled, which isn't an option right now. Or to bring all the wood into our house to acclimate. Although wouldn't it just revert back to the outdoor environment once I take it into the shop?
Am I worrying about this too much, or should I not try and sell someone a bed that may warp?
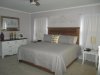
I recently had someone ask me to make a bed from a different design where the frame and headboard are connected. My concern is that the wood movement will cause the bed to not work out as nicely for these people as the other design did for us. I know you are supposed to acclimate the wood in its final environment before working with it, but how do I do that with an entire bed? The only things I know to do are to make the shop climate controlled, which isn't an option right now. Or to bring all the wood into our house to acclimate. Although wouldn't it just revert back to the outdoor environment once I take it into the shop?
Am I worrying about this too much, or should I not try and sell someone a bed that may warp?