I have a 14" Delta Band saw and will be cutting a curvy fence picket out of some
The tightest radius is likely to be 1.25" At present, I've only got a 1/2" wide blade in the saw and would like an excuse to purchase a new blade and cutting sixty-one of these pickets should serve that purpose.
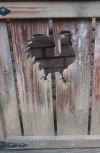
So far, I've gotten along well enough (ten plus years?) without buying any blades ('till I got this 1/2" number) and did cut all the pickets I'll be replacing with whatever smaller blade I may have hanging about (just have to recall where I put 'em, of course).
But, since I first did that deck, I signed up here and thought to ask for an experienced opinion as to, not only the size, but perhaps a good type and quality of blade as well.
Anyone?
Then, I noticed this question has been (last month) asked and answered. Even with a video. It popped up right after I saved my post! "
Bandsaw blade choice for curves only
Replies7Views389
Jun 6, 2024
bob vaughan
B
"
5/8 in. x 5-1/2 in. x 6 ft. Pressure-Treated Pine Dog-Ear Fence Pickets
The tightest radius is likely to be 1.25" At present, I've only got a 1/2" wide blade in the saw and would like an excuse to purchase a new blade and cutting sixty-one of these pickets should serve that purpose.
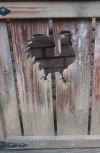
So far, I've gotten along well enough (ten plus years?) without buying any blades ('till I got this 1/2" number) and did cut all the pickets I'll be replacing with whatever smaller blade I may have hanging about (just have to recall where I put 'em, of course).
But, since I first did that deck, I signed up here and thought to ask for an experienced opinion as to, not only the size, but perhaps a good type and quality of blade as well.
Anyone?
Then, I noticed this question has been (last month) asked and answered. Even with a video. It popped up right after I saved my post! "
Bandsaw blade choice for curves only
Replies7Views389
Jun 6, 2024
bob vaughan
B
"
Last edited: