I picked up one of the LN 60 1/2R rabbet planes on sale and have been using it alot. The last project was a dowel jig that I made for a ww buddy at work. He needed some contrasting dowels. I knew his pain because I like to do the same. Like cherry table with walnut dowels pinned thru the mortices. BUT -- If you have ever cut up dowel sticks on your bandsaw, you have watched them dance around like little grasshoppers. It is pretty spooky. A coping saw is not much better because they usually break. Anyway, I came up with this little jig which began life as a 2x4. The little dowel pins just fall into the box on the end after they are cut. Pretty neat, huh? Well the challenge is the Vee groove. It is hard to do with a router, but is a snap with the LN rabbet plane. I started with a saw kerf from the backsaw. Then I used the plane and alternated sides. The Vee groove took about one minute and came out perfectly. Hand tools rock!
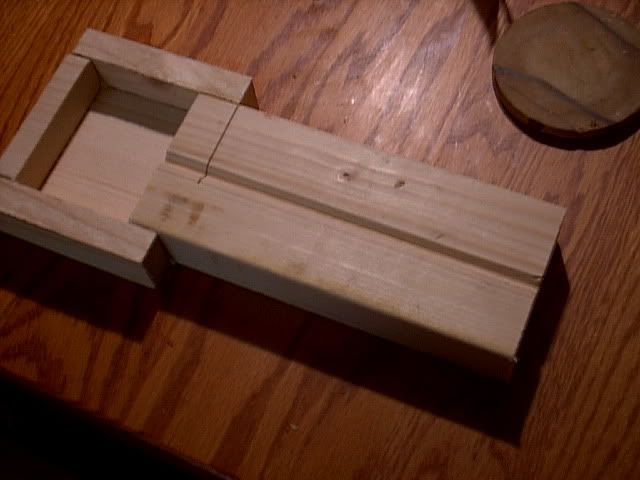